Материалы
и методы , применяемые при
изготовлении стеклопластика.
Источник : The Elements of Boat Strength , 2000
Автор : Dave Gerr
Перевод С.Б.
(Данный
материал представляет собой отрывки из трех разных глав книги ,
поэтому мне не удалось придать ему
гладкую логическую структуру. С.Б. )
Производство современных корпусов из стеклопластика основано на принципе , известном с античных
времен - добавка в глину или гипс всего двух процентов волокнистой массы резко повышает их прочность , снижает
образование трещин при ударах и изгибах . Чем больше волокна вы кладете в пропорции к связующему , тем прочнее
получается их комбинация . Поэтому применение композитных материалов насчитывает
уже несколько тысячелетий .
Другим примером композита , который сопровождает нас на протяжении более трех тысяч лет , является папье-маше
. Древние египтяне пользовались этим методом для изготовления саркофагов
- ламинированных гробниц . В восемнадцатом веке в Европе таким способом
делали шкатулки и мебель . А во время Второй Мировой ,
верите
или нет , этот метод использовался для производства авиационных топливных баков . У папье-маше есть свои
недостатки - низкая прочность , горючесть , и что хуже всего - нестойкость к влаге . Пока изделие
находится под слоем лака или краски в сухой атмосфере - все обстоит прекрасно , однако стоит ему только намокнуть - это и будет его
концом .
Как ни странно , но главным толчком к разработке современных композитов
оказалось развитие электротехнической
индустрии . Старые изоляционные материалы -гуттаперча , вощеная бумага , шеллак и керамика , которые годились
для применения в телеграфных линиях ,
уже не справлялись со своими задачами , когда речь зашла о высоких токах .
Бельгийский химик Лео Бакеланд в 1906 году открыл реакцию , в результате которой взаимодействием фенола с
формальдегидом получалась прочная и водостойкая смола . Но только много месяцев спустя он понял , что если
добавить в хрупкую смолу волокно (в молотом виде) , это значительно повышает ее прочность . Таким образом и
появился бакелит - первый "современный" композит , ознаменовавший собой начало
пластмассовой революции . В промежутке между двумя мировыми войнами домашняя
утварь и электрооборудование - все имели бакелитовые ручки , кнопки , корпуса и изоляцию .
С того момента начался непрерывный рост прочности , жесткости и атмосферостойкости этих смол . Были
перепробованы все возможные варианты композиций со всеми видами волокон - от целлюлозы до асбеста . Да-да , составы на
основе фенольных смол и асбеста были популярны в конце Второй Мировой Войны . Известный под названием Durestos , этот
материал обладал очень высокими характеристиками , в некоторых отношениях не уступая современным
пластикам . Тогда никто не задумывался о связанном с этим риском для здоровья , поэтому всем нам повезло , что этот
материал не получил распространения .
В конце концов мы пришли к тому , что самым удобным и экономичным методом
для постройки корпуса судна оказалось применение стеклянных волокон
и полиэфирной смолы .
Процесс , который при этом используется , в точности повторяет древний способ изготовления папье-маше
. При постройке саркофага древние египтяне изготавливали матрицу из гипса или глины , которую затем покрывали
изнутри разделительным составом - льняным маслом или мылом . Следом в эту матрицу укладывались чередующиеся
слои клеящей пасты и бумаги и плотно прижимались . Процесс продолжался до достижения необходимой толщины .
Большинство современных серийных стеклопластиковых лодок
делается по точно такой же
методике . При постройке корпуса первым делом изготавливается матрица ,
которая покрывается изнутри разделительным составом (сегодня это воск) . Затем в нее до достижения
нужной толщины кладутся чередующиеся слои стекломатериалов разных типов и
полиэфирной смолы . Так что , возможно , "современная" технология не так уж
и современна , как мы об этом думаем .
Ручное формование , вакуумное
прессование и напыление рубленого
волокна .
То , что было описано выше , известно
как ручной способ формовки
стеклопластика . Он имеет самое широкое
распространение и являет собой
наиболее успешный метод , каким можно получить корпус .
Существуют также еще два
альтернативных метода . Один из них
представляет тот же ручной способ , но
немного усовершенствованный . Весь
технологический процесс протекает как
обычно , однако после укладки всех
слоев , пока смола еще не
полимеризовалась , на матрицу с
корпусом накидывается вакуумный мешок
(на практике - большой лист пленки) и
герметизируется лентой . Воздух
частично откачивается вакуумным
насосом , что приводит к тому , что
воздух снаружи пленки оказывает
высокое равномерное давление на нее
, а следовательно , на весь ламинат в
целом . При этом получается
необыкновенно плотный , прочный и
ровный пластик , который по прочности
значительно превышает стеклопластик
ручной формовки . Это происходит
благодаря тому , что
стеклопластик , получаемый методом
вакуумного формования , содержит
больше стекла в пропорции к смоле . А
чем больше волокна содержит ламинат (при
соблюдении технологии) - тем он прочнее
. Атмосферное давление равно примерно
101 кПа . Если при формовании корпуса
уменьшить давление под пленкой всего
на четверть - до 76 кПа , в результате мы
получим давление на нее снаружи в 25 кПа
. Надеюсь , вы поняли , что это означает ? 25
кПа - это 2 600 кг/м2 . Если мы возьмем для
примера 28-футовый корпус с площадью
поверхности в 45 кв.м , суммарное
давление будет равным 116 тонн ! На
практике давление обычно бывает в
диапазоне 48-62 кПа .
Другой крайностью является
изготовление стеклопластика при
помощи напыления рубленого волокна .
Используя специальный пистолет , на
поверхность матрицы выдувается поток
мелко нарубленного стекловолокна в
смеси с жидкой смолой . То , что
получилось , затем прикатывается
вручную валиком . Поскольку волокна
короткие , хаотично ориентированные и
контроль за толщиной наносимого слоя
отсутствует , такой стеклопластик
получается менее плотным и прочным ,
чем при ручном формовании , и гораздо
менее прочным , чем при вакуумном
формовании . Однако данный способ
изготовления корпуса самый быстрый и
дешевый . Означает ли это , что он
плох ? Нет , не означает , просто
покупатель всегда получает то , за что
он заплатил . Понятно , что получаемый
таким методом корпус должен обладать
увеличенной толщиной обшивки , а стало
быть и весом для достижения той же самой
прочности . Однако даже в этом случае
запас его прочности и долговечность
будут куда меньше , чем у качественно
отформованного ручным методом корпуса
. Поэтому , если не ставить цель
достижения высоких скоростей и хранить
лодку на берегу - правильно
спроектированный корпус такой
конструкции может вполне устроить .
Достоинства и недостатки трех методов .
Ознакомившись с этими тремя способами
формования , мы можем оценить их плюсы и
минусы . Ручной способ является
фактически промышленным стандартом .
Правильно изготовленный им корпус
имеет гладкую ровную поверхность
снаружи и внутри и равномерную толщину
на каждом отдельном его участке .
Механические свойства такого корпуса
более чем достаточны для большинства
обычных судов . Вакуумно-формованный
ламинат более плотный , содержит
меньшее количество смолы в пропорции к
армирующему стекловолокну . При той же
толщине прочность такого
стеклопластика выше . Хотя в
большинстве случаев это и ни к чему , однако
конструктор и изготовитель могут
снизить вес или повысить скорость (или
то и другое одновременно) , применив
вакуум . Эта технология повышает
стоимость работ (обычно меньше , чем
ожидается) , а толщина оболочек
сэндвичевых конструкций может
оказаться слишком тонкой , чем это
ьребуется для малых и быстроходных
судов .
Стеклопластик , получаемый
напылением - самый дешевый , а из-за
повышенного весового содержания
смолы - самый непрочный . Этот метод
годится для серийного производства
корпусов , для которых вес и скорость не
являются главными приоритетами . Таким
способом можно успешно изготавливать
внутренние и второстепенные
компоненты для корпуса ,
отформованного ручным методом .
Естественно , те же самые компоненты
будут иметь меньший вес , если их
изготовить вручную или применить
вакуум , однако при серийном
производстве получаемая таким образом
экономия вполне оправдывает этот шаг .
Компоненты стандартного стеклопластика
С той поры как стеклопластик впервые
начал применяться как материал для
постройки корпусов лодок на рубеже 40-50-х
годов , существует всего три
стандартных материала , обычно
изготовленных из стекловолокна
категории Е (обыкновенное ,
электротехническое или
строительное) .
Стекломат
Стекломат , он же просто мат ,
представляет собой стекловолокна ,
нарубленные мелкими кусками длиной от
12 до 50 мм и склеенные друг с другом
временным связующим - эмульсией . Из-за
того , что волокна короткие и
ориентированы хаотично , мат не
отличается прочностью. Однако он легко
пропитывается смолой , так как является
мягким , толстым и рыхлым , похожим
на губку при пропитывании . Мат хорошо
использовать для клеевого соединения
слоев из других видов стекломатериалов
и заполнителей . Поэтому самый
популярный способ формования корпуса -
это укладка чередующихся между собой
слоев ровинга и мата .
Тканый ровинг .
Тканый ровинг - тяжелая грубая ткань ,
состоящая из прядей стекловолокна .
Благодаря тому , что волокна имеют
большую длину и ориентированы в
перпендикулярных направлениях , ровинг
представляет собой очень прочное
армирование . При равном весе ,
отформованный из одного только ровинга
стеклопластик обладает в два раза
большей прочностью , чем стандартный
стеклопластик из ровинга и мата .
Однако , чтобы изготовить качественный
ламинат из чистого ровинга , требуется
высокая квалификация и внимание . Без
мягкого рыхлого материала , каким
является мат , сложно добиться ,
чтобы сравнительно твердые и плоские
слои ровинга надежно склеились друг с
другом . Поскольку стеклопластик из
ровинга с матом на практике обладает
достаточными качествами для обычных
лодок , мало кто из производителей идет
на дополнительные расходы .
Стеклоткань .
Настоящая стеклоткань представляет
собой очень прочный материал . Из-за
своей дороговизны она применяется
практически исключительно в
конструкциях небольших лодок и для
отделочных работ . В отличие от ровинга
ткань имеет очень мелкую текстуру и
часто используется при формовании как
наружный слой для укрытия грубой
поверхности ровинга и мата . К примеру ,
один-единственный слой стеклоткани
изнутри корпуса позволяет получить
красивую гладкую поверхность . Как
следствие , тонкую стеклоткань часто
именуют отделочной .
Стандартная полиэфирная смола .
Самой распространенной смолой для
изготовления стеклопластика является
полиэфирная . Смола в жидком виде
смешивается с катализатором и
акселератором , при этом происходит
реакция полимеризации . Это означает ,
что молекулы пластика образуют друг с
другом связи , превращаясь в жесткую
структуру . В идеале весь корпус
представляет собой одну молекулярную
цепь .
Катализатор .При всем разнообразии
катализаторов , самым распространенным из
них является продукт реакции
метилэтилкетона с перекисью водорода ,
или пероксид (MEKP=methyl ethyl ketone peroxide) .
Это очень опасное вещество - оно
вызывает сильную коррозию и при
попадании на кожу его необходимо смыть
как можно скорее . Что еще интереснее -
это агрессивное вещество может
привести к взрыву . Когда акселератор ,
применяемый для ускорения процесса
полимеризации , вступает в прямой
контакт с пероксидом - если не
взрыв , то как минимум пожар вам
обеспечены . Как следствие ,
большинство смол , применяемых в
судостроении , поставляются с уже
введенным акселератором .
Стандартный процесс формования
стеклопластика.
В течение последних сорока лет
стандартным и самым простым способом
формования корпуса является укладка
чередующихся слоев тканого ровинга и
стекломата . Как и в случае с
заполнителем , мат между слоями
ровинга улучшает их адгезию друг к
другу . Однако в остальных случаях мат
не должен содержать смолы более , чем
это необходимо .
Чаще всего
производители приобретают мат и ровинг
в виде уже пристеганых или приклееных
друг к другу слоев того и другого ,
называя это комби-матом или фаб-матом .
Такие материалы снижают трудозатраты ,
позволяя за одну операцию укладывать
сразу два слоя .
Соотношение стекловолокна и смолы , или
, как его еще называют - содержание
стекла , для стандартного метода с
использованием ровинга и стекломата ,
составляет около 35% по весу .
Стеклопластик на базе одного только
стекломата содержит около 28% стекла ,
для стеклопластика из одного ровинга
эта цифра составляет 40%. Еще раз
нелишним будет напомнить , что чем выше
содержание стекла (в пропорции к смоле) , тем выше будут
механические свойства ламината (прочность).
Особенности конструкции
стеклопластикового корпуса
Места концентрации напряжений .
Из-за того что стеклопластик довольно
гибкий материал и в большинстве
случаев толщина его небольшая , он
может испытывать многократные изгибы в
местах концентрации напряжений ,
резких углов , установки оборудования ,
болтов и другого крепежа . Поэтому
крайне важно иметь в таких местах
подкладочные пластины , помогающие
распределить нагрузку ; для вклеивания
стрингеров , переборок и прочих
элементов мокрый угольник должен
обладать большой площадью ; все
переходы от одной толщины к другой
должны быть плавными .
Все углы стеклопластиковой
конструкции и ее вторичных клеевых
соединений должны иметь радиус или
галтель - стеклопластик не терпит
острых углов . При выполнении
внутренних углов следует использовать
галтель из пенопласта , бальзы или
шпатлевки . В равной степени это
относится к углам транца , форштевню ,
вклеиванию переборок , стрингеров ,
оборудования и встроенных баков .
Переходы толщин заполнителя .
Из-за того что толщина стеклопластика в
сэндвиче меньше чем у сплошного ,
распределение нагрузок и устранение
мест их концентрации здесь особенно важны .
Согласно требованиям Береговой Охраны
США и Американского Бюро
Судоходства , переход от области ,
содержащей заполнитель к сплошному
стеклопластику должен иметь плавную
клинообразную форму .
Вторичные клеевые соединения .
При правильном процессе изготовления
стеклопластикового корпуса он
формуется одним непрерывным процессом
, где перерывы между укладкой слоев не
должны превышать 16 часов (чем меньше ,
тем лучше).
Еще лучшее правило : время до укладки
следующего слоя не должно превышать
удвоенного времени желатинизации
смолы . В таком случае смола этого слоя
образует химические связи с предыдущим
.
При соблюдении данного условия все слои (в той или
иной степени) будут полимеризоваться
одновременно , образуя единое целое
посредством первичных связей .
Естественно , переборки , элементы
жесткости и внутренняя обстройка будут
установлены позже - после полного отверждения корпуса . Мокрый
угольник , при помощи которого будут
устанавливаться эти элементы , будет
являть собой вторичные связи , по
прочности не идущие ни в какое
сравнение с первичными .
Образование химических связей в этом
случае незначительно .
Хотя эта проблема и неизбежна , большой
опасности она не представляет - для
образования качественного соединениянеобходимо только
выполнить определенные требования . Поверхность должна быть
слегка зачищена ( быть грубой , чтобы
дать смоле возможность "зацепиться")
, а пыль удалена при помощи пылесоса .
Затем ее следует протереть и
обезжирить тряпкой , смоченной в
ацетоне или стироле . Если ламинату
больше трех месяцев , стирол
предпочтительней - он размягчает
старую смолу , тем самым улучшая
адгезию . Только тогда можно
пропитывать материал угольника ,
прикатывать его и прижимать . Большинство
производителей применяют одну и ту же
полиэфирную смолу как для формования
корпуса , так и для установки
компонентов . Если это делается со всей
тщательностью , претензий нет ,
однако лучшие фирмы для всех
конструктивных соединений
применяют винилэфирную смолу .
Соединения при этом получаются более
прочные и долговечные .
Что бывает , когда эти шаги не
соблюдаются , можно наблюдать на
фото корпуса , поступившего в ремонт
. Попав в шторм , он буквально начал
разваливаться на части . Переборка (элемент
жесткости) была выдернута из корпуса
одной рукой . Фирма-изготовитель не
только не потрудилась обеспечить
качество соединений , но и не применила
пенопластовые прокладки (или хотя бы
галтели) для придания радиуса
угольнику .
Недопустимость незащищенной древесины
.
В стеклопластиковых корпусах часто в
качестве заполнителя применяется
фанера или древесина . Внутри
практически всегда присутствуют деревянные
подкладки и панели - для крепления
оборудования и интерьера . Если
древесина играет роль коструктива (в
отличие от обстройки) , она не должна
оставаться незащищенной . Каждый деревянный
элемент должен иметь покрытие . Если
этого не будет , древесина не только
может загнить , но что гораздо хуже
- она будет многократно забухать и
высыхать вместе с регулярными
изменениями влажности . В конце концов (а
иногда и довольно скоро) дерево
растрескивается и отделяется от самОй
стеклопластиковой конструкции , что
очень плохо . Как правило , деревянные
элементы , находящиеся в
контакте со стеклопластиковой
конструкцией , обильно покрываются
смолой и затем гелькоутом из
распылителя . Нужно иметь очень
наметанный глаз , чтобы обнаружить
элементы , замаскированные таким
образом . Если дерево не имеет местного
ламинированного или иного
конструктивного крепления к
стеклопластику , достаточно посадить
его на морской герметик и обработать
антисептиком или покрасить - одним
словом , покрыть чем-нибудь со всех
сторон , и сделать это на совесть .
Гелькоут и борьба с проявлением
текстуры .
Обычно процесс формования
стеклопластикового корпуса начинается
с нанесения разделительного воска на
внутреннюю поверхность матрицы и затем
покрытия ее поверхности гелькоутом из
распылителя - толщиной 0.5-0.76 мм . При
большей толщине гелькоут склонен к
образованию трещин , при меньшей
страдает качество поверхности .
Гелькоут представляет собой смолу
высокого качества с введенным цветным пигментом . Затем ему дают частично
полимеризоваться (три-четыре часа , в
зависимости от смолы) . Следующим шагом
на частично вставший гелькоут кладется
слой мата . Для большинства малых судов
длиной 7.5-9 м вес этого мата составляет
300-450 г/м2 . Для лодок меньшего размера
вес мата как правило 230-300 г/м2 . Этому слою
дают полимеризоваться (обычно до утра )
, после чего укладывается оставшийся
конструкционный пластик . Опять же ,
если длина корпуса превышает 9 м , следующим слоем идет мат весом 300-450 г/м2
, а для лодок менее 7.5 м - 230 г/м2 .
Назначение стекломата - избежать
проявления грубой текстуры
нижележащего конструкционного
материала , каким обычно выступает
ровинг . Мат эту задачу выполняет ,
потому что он мягкий , рыхлый и содержит
большое количество смолы (или мало
стекла , что одно и то же) .
Большинство производителей лодок
длиной менее 7.5 м старается укладывать
600 и более г/м2 стекломата между гелькоутом и
конструкционным ламинатом . Такова , к
сожалению , необходимость и в
большинстве случаев приходится с этим
мириться (
при малой прочности мат добавляет
значительный вес ) . Еще надо иметь в
виду , что чем более мелкую текстуру
имеет конструктивный материал , тем
меньше его тенденция проявлять ее на
гелькоуте . Поэтому некоторые из легких
стеганых матов могут помочь снизить
количество стекломата в наружном слое
.
Как вариант - если основную часть
ламината будет составлять стандартный
комби-мат 24-15 (813 г/м2 ровинга + 450 г/м2
стекломата) , его можно укладывать
непосредственно на внешний слой мата
весом 470 г/м2 . Это также позволит
снизить эффект проявления текстуры
.
При отверждении смолы выделяется тепло
- естественный продукт химической
экзотермической реакции . Чем выше
температура этой реакции при
полимеризации , тем большую усадку
получит ламинат после охлаждения .
Усадка способствует проявлению
текстуры . Как из этого следует , ее
можно снизить :
- путем применения самых медленных смол
, какие только допустимы на практике
- путем снижения толщины внутренних
оболочек
- путем поддержания низкой температуры
в рабочем помещении .
Это весьма деликатный вопрос и лучше
всего проконсультироваться по у
производителя смолы - какой процесс
и композиция более всего годится для
конкретной смолы .
Смола : хранение и смешивание .
При том , что стекломатералы для
формования стеклопластика не имеют
срока хранения , сами смолы
представляют собой довольно летучие
соединения . Я часто поражаюсь тому ,
как безответственно некоторые
производители относятся к хранению
и смешиванию смолы . Всегда следите за
сроком годности смолы и не пытайтесь ее
использовать после его истечения ,
иначе вам придется об этом пожалеть .
Смола должна храниться в прохладном
помещении , куда не попадает прямой
солнечный свет . Емкости должны быть
закрыты так , чтобы в них не могли
проникнуть воздух и влага и даже в
частично использованных бочках надо
стараться свести количество
конденсата к минимуму . Крайне важно
, чтобы смола перед розливом и
использованием была тщательно
перетерта в емкости хранения .
Многие необъяснимые случаи брака при
формовании явились результатом
игнорирования этих простых правил
.
Современные ламинаты : волокна и
смолы .
За последние пятнадцать лет в обиход
вошло большое количество новых тканей и волокон
. Их применение
позволяет конструктору и строителю
создавать крепкие ,
жесткие и легкие корпуса . Как правило , такие ламинаты обходятся дороже , а
временами значительно дороже .
Ранее уже говорилось , что обычный
стеклопластик являет собой стекломат ,
стеклоровинг и стеклоткань . Все эти
материалы изготовлены из
стекловолокна категории Е (E = Electrical =электротехническое)
,
являющегося стандартом в
судостроении и при изготовлении
конструкций . Стекловолокно категории S
или S2 (S = Structural = конструкционное) по своему химическому составу
идентично категории Е , однако это
авиационное волокно . Отдельные
волокна имеют меньший размер , содержат
меньше примесей и меньше дефектов . Это
значительно повышает прочность
отдельных волокон и в конечном итоге
всего ламината в целом .
Вместо электротехнического стекловолокна
аналогичным образом могут быть
использованы кевлар , спектра и
углеволокно . Они обладают в 3-10 раз
более высокой прочностью и жесткостью ,
позволяя получить намного более
прочные ламинаты . Жесткость
измеряется величиной , известной как
модуль упругости , поэтому эти
современные материалы часто именуются
высокомодульными .
Современные типы стекломатериалов :
однонаправленные , биаксиальные и
стеганые .
Однонаправленные материалы (Uni-Di , UD) .
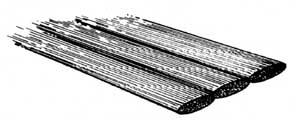 |
У однонаправленных тканей все
пряди плотно уложены в одном
направлении . Изгибы волокон
отсутствуют , а мест
концентрирации смолы мало . |
Еще один способ повысить механические
свойства ламината состоит в том ,
чтобы избавиться от изгибов вверх-вниз отдельных
волокон и выровнять их в том
направлении , где необходима прочность
. С этой целью производится укладка
волокон только в этом направлении .
Материал имеет форму рулона , в котором
отдельные волокна связаны друг с
другом либо прошивкой , либо какой-либо
эмульсией . Такой тип материала
называется однонаправленным .
Поскольку в этом случае волокна не
изгибаются вверх-вниз , переплетаясь с
поперечными , данный материал обладает
более высокой прочностью , чем даже
ровинг (состоящий из тканых пучков
волокон) . Все волокна ориентированы
одинаково , поэтому максимальная
прочность также будет только в этом
направлении . Плюс ко всему отдельные
волокна лежат близко друг от друга и
легко пропитываются смолой . Это
означает , что весовое отношение
волокна к смоле будет очень высоким -
вакуумированный ламинат из
однонаправленного стекловолокна
содержит 55-60% стекла , а в лучших
случаях - 65-70% .
Биаксиальные ткани .
К сожалению , на практическом пути
применения чистых однонаправленных
материалов лежат два препятствия .
Первое и наиболее явное - прочность
только в одном направлении . Чтобы его
обойти , приходится укладывать
однонаправленный материал в виде
множества слоев под разными углами .
Первый слой укладывается , к примеру
, под углом 45 градусов к продольной оси
корпуса , второй укладывается под
противоположным углом , как в случае
диагональной обшивки . Это именуется ±45
, +45/-45 или просто 45/45 . Как вариант , слои
могут лежать вдоль и поперек
продольной оси , что именуется 0/90
. Как и в случае с комби-матом (стекломатом , к которому пристеган
тканый ровинг) , производители
стекломатериалов предлагают
варианты , совмещающие в себе
однонаправленные слои . Это позволяет
уложить два слоя за одну операцию .
Такой тип тканей называется
биаксиальным (даже если он имеет
конструкцию 0/90) . Существуют также
триаксиальные и квадроаксиальные
ткани . Триаксиальные могут иметь
конструкцию +45/-45/0 , где все три слоя
простеганы воедино и имеют вид рулона .
Комбинируя биаксиальные ткани
конструкции 45/45 с тканью конструкции 0/90
, можно получить равную прочность во
всех направлениях . Хотя это будет и
прочнее , чем тканый ровинг , чистый
однонаправленный ламинат в
направлении укладки все равно обладает
более высокими характеристиками .
Стеганые маты .
Второй проблемой применения
однонаправленных материалов является
отсутствие мата между слоями ,
обеспечивающего их надежную связь .
При тщательном подходе , с применением
вакуумирования и эластичной ,
заполняющей пустоты смолы , такой
вариант годится . Тем не менее для
большинства случаев все-таки
желательно некоторое количество
стекломата . Его количество - очень
деликатный вопрос . Во-первых , мат - это
непрочный тяжелый материал , поэтому
его надо использовать по минимуму . Во-вторых
, большинство стекломатов несовместимы
с высокопрочными смолами . Чтобы
разрешить это противоречие ,
производители предлагают материал ,
представляющий биаксиальную ткань с
пристеганным к ней тонким слоем мата ,
называя это стеганым матом (stitch-mat).
Типичным стеганым матом является Hexel
Knytex DBM 1708 . Это биаксиальный материал 45/45
(что означают буквы "DB") из двух
однонаправленных слоев весом по 8.5
унций (что в сумме дает "17") с одним
слоем пристеганого мата весом 0.75 унц. (округлено
- "08") . Если перевести в
метрические единицы , получим два
слоя по 288 г/м2 со слоем мата весом 25 г/м2 .
Мат специально не имеет какой-либо
связующей эмульсии либо замасливателя
, которые могут оказаться
несовместимыми с прочными смолами .
Стеганые маты существуют самых разных
видов - 0/90 , 45/45 , с матом разной толщины и
веса , что дает возможность максимально
использовать свойства современных
материалов и смол без лишних
трудозатрат . Укладка такого материала
эквивалентна сразу трем слоям - двум
однонаправленным и одному мата .
Даже применяя обычное
электротехническое волокно в виде стеганого
мата , можно добиться значительного
повышения прочности . Прочность на
изгиб , к примеру , вышеупомянутого
DBM 1708 составляет 434 МПа , в то время как
стандартный ламинат из мата и ровинга
демонстрирует всего 206 МПа .
Применяемые типы смол
Полиэфирная смола .
Нет никакого смысла в применении
современных видов тканей и
высокомодульных материалов со
стандартной полиэфирной смолой . Это
универсальная смола , которая
является стандартом в промышленности
на протяжении уже многих лет . Ее недостаток
состоит в том , что она довольно
хрупкая - при повышенных нагрузках она
покрывается трещинами , вместо того
чтобы растягиваться и затем принимать
свою первоначальную форму . Прежде чем
треснуть , ортофталевая полиэфирная
смола удлиняется примерно на 2 % при
прочности на разрыв в 65 МПа . Это
говорит о том , что когда тонкие
высокомодульные волокна и современные
ткани будут еще тянуться , достигая
своего рабочего диапазона , сама смола
уже растрескается.
Другим видом
полиэфирной смолы является
изофталевая . Она немного эластичней и
обладает повышенной химической
стойкостью , т.е. менее чувствительна к
осмотическим явлениям и химическим
веществам , содержащимся в воде .
Изофталевая смола тянется на 2.5% прежде
чем растрескаться и обладает примерно
такой же прочностью , как и
ортофталевая . Стеклопластик на
изофталевой полиэфирнрй смоле ,
отформованный при помощи вакуума с
использованием биаксиального
материала со стекломатом (Е)
позволяет получить достаточно прочный
корпус , который прочнее , чем
стандартный ламинат из мата и ровинга .
Увеличение стоимости по сравнению с
вариантом мат-ровинг-ортофталевая
смола довольно незначительное .
Винилэфирная смола .
Чтобы максимально использовать
прочностные свойства современных
волокон , необходима смола ,
обладающая высокой прочностью и при
этом способная тянуться. В
судостроении такими смолами чаще всего
выступают винилэфирная и эпоксидная .
Винилэфирная обладает гораздо большей
эластичностью , чем любая из
полиэфирных - в среднем она тянется на 5%
, прежде чем треснуть и обладает
прочностью на разрыв в 82 МПа . Это
означает , что стеклопластик на основе
такой смолы будет много прочнее
полиэфирного и прочность
соединения оболочки с заполнителем
будет выше . Винилэфирная смола
обладает куда более высокой химической
и осмотической стойкостью , чем любая
из полиэфирных смол.
Еще одним достоинством винилэфирных
смол является их совместимость с
материалами , которыми обработаны
стандартные стекломаты и с
оборудованием и технологиями ,
применяемыми при работе с полиэфирными
смолами . Те , кто привык работать с
полиэфирной смолой , не испытывают
каких-либо трудностей при переходе на
винилэфирные и обратно . Что более
ценно - винилэфирные обладают
уникальным свойством образования
хороших клеевых соединений с
полиэфирной смолой , равно как и
наоборот . Все это позволяет очень
гибко организовать процесс
производства . В большинстве случаев
стеклопластик на винилэфирной смоле
с использованием биаксиального
материала со стекломатом (Е)
либо высокомодульных тканей обладает
такой прочностью , которая только может
потребоваться на практике .
Эпоксидные смолы . Смолы , обладающие еще более высокой
прочностью - эпоксидные . Они тянутся
как правило более чем на 5% , а прочность
на разрыв составляет 86 МПа . Химическая
стойкость у них еще выше , чем у
винилэфирных . Благодаря своей
способности заполнять мелкие пустоты и
высокой эластичности , эпоксидные
смолы обладают самой высокой
прочностью на отрыв из всех
стандартных смол . Как следствие ,
стеклопластик на основе эпоксидной
смолы может с успехом формоваться без
использования стекломата вообще (хотя
для образования соединения
сэндвичевого заполнителя с оболочкой и
требуется предназначенный для
эпоксидной смолы мат либо специальная
шпатлевка ) . Если из ламината убрать
стекломат , это позволит добиться
наивысшего содержания в нем стекла или
иного волокна , получив в итоге
стеклопластик с самыми высокими
механическими характеристиками .
Качественно отформованный вакуумом
ламинат из конструкционного стекловолокна
(S) обладает прочностью на изгиб в 586 МПа .
Это равноценно прочности нержавеющей
стали при в пять раз меньшем весе и
отсутствии коррозии .
Стеклопластик такого рода весьма
недешев - как по стоимости
материалов , так и по квалификации
работников и проектировщиков .
Применяемое при этом оборудование
плохо совместимо с полиэфирным
техпроцессом . Поэтому на практике
эпоксидные смолы более всего находят
применение в области достижения предельных скоростей , в
военной и спасательной технике .
Высокомодульные ламинаты
Ранее мы говорили толко о стандартных
промышленных стеклопластиках -
стекловолокно подразумевалось
электротехническое (Е) , а смола -
полиэфирная . В третьей главе были
рассмотрены преимущества
высокомодульных волокон в комбинации с
винилэфирной и эпоксидной смолой . При
применении этих материалов с одной стороны
поверхности корпуса увеличение прочности
будет весьма незначительным :
только в сэндвичевой конструкции они
показывают то , на что способны . При
большей прочности и меньшей толщине (а
стало быть массе) , они имеют вид легких
тканей , позволяющих гибко
организовать процесс формования . Для
расчета толщины корпуса и палубы с
применением этих волокон можно
воспользоваться следующими правилами .
Толщина стеклопластиковой оболочки
при переходе на конструкционное (S)
волокно и винилэфирную смолу .
Используется конструкционное (авиационное)
стекловолокно в виде
однонаправленных , би- и три-аксиальных
матов . Толщина расчитывается
согласно стандартной сэндвичевой
методике , затем толщина оболочек (но не
заполнителя) уменьшается на 10
процентов . Вакуумирование оболочек и
заполнителя желательно , однако
приемлемо и качественное ручное
формование . Смола - винилэфирная или
эпоксидная .
Внутренняя кевларовая оболочка .
Кевлар используется только для
внутренних оболочек сэндвича . Он
обладает очень высокой стойкостью к
истиранию , поэтому имеется тенденция
располагать его и снаружи . К сожалению ,
при высокой прочности на разрыв кевлар
обладает весьма посредственной
прочностью на сжатие . А так как при
ударе именно наружный слой испытывает
сжатие , там ему не место . Возможен
вариант использования кевлара снаружи в
качестве дополнения к обычному
ламинату , и только с целью
повышения износостойкости . При
использовании кевлара изнутри (внутренняя
оболочка работает на растяжение , а это
и есть его сильная сторона )
расчитывайте
толщину внутренней оболочки согласно
стандартной методике и уменьшите ее (но
не заполнитель) на 15 процентов . Опять
же - вакуумирование оболочек и
заполнителя и винилэфирная или
эпоксидная смола .
Следует добавить , что кевлар не только
дорогой , но и сложный в работе
материал . Он требует иных методов и
инструментов для резки , его труднее
равномерно пропитать смолой , чем
большинство других видов тканей .
Стекло снаружи , кевлар внутри .
Самая высокая прочность при наименьшем
весе достигается путем применения ваккумным
методом конструкционного стекловолокна для наружной оболочки сэндвича и
кевлара - для внутренней .
Применение стеганых матов при
вакуумном формовании с
винилэфирной смолой
Конструкционное стекловолокно и
кевлар стОят гораздо дороже , чем
электротехническое . Для
большинства же обычных судов (и даже очень
крепких) применение стандартных
стеганых однонаправленных материалов
из электротехнического волокна с
винилэфирной смолой позволяет
получить легкий , прочный и
ремонтопригодный корпус (в
особенности с применением вакуумного
формования). При расчетах толщины
стеклопластика используется
стандартная для сэндвича методика и
удельный вес стекла определяется по
ней . При вакуумном формовании реальная
толщина оболочки будет несколько
меньше - пластик будет плотнее и
содержать меньше излишков смолы. Как
результат , он будет более легким и
прочным .
Ориентация волокон стеганых матов .
Стандартный ламинат , состоящий из мата
с ровингом , имеет примерно равную
прочность во всех направлениях . Вне
зависимости от вида применяемых смол ,
биаксиальные ткани типа 45/45 или 0/90
имеют максимальную прочность только в
двух направлениях . Прочность по
диагонали у них низкая . Следовательно ,
при формовании требуется чередовать
между собой материалы типов 45/45 и 0/90 .
Получившийся ламинат будет обладать
практически равной во всех напрвлениях
прочностью .
Графитовое и угольное волокно .
Эти правила не распространяются на
графитовые и угольные волокна (в
принципе , это один и тот же материал
, однако графит содержит меньше
примесей и более прочный ). Хотя
углепластик и обладает очень высокой
жесткостью , он крайне мало растяжим (т.е.
перед тем как разрушиться , тянется совсем немного). Это делает
ламинаты на его основе хрупкими и
склонными к внезапному и обширному
разрушению . Их применение имеет
реальный смысл при проектировании
экстремальных конструкций . Расчеты
должны быть очень тщательными и в
данной книге они не рассматриваются .
Испытание сэндвича на прокол .
Все сэндвичевые ламинаты , как
стандартные на базе полиэфирной смолы
и электротехнического волокна , так
и на базе винилэфирной смолы и конструкционного волокна
или
кевлара , имеют одну одинаковую
проблему : их тонкие наружные слои можно проткнуть насквозь .
Некоторые закрывают на это глаза и идут
на риск с такой оболочкой , которая в прочих ситуациях выглядят
достаточно прочной . Однако так
поступать не следует - всегда надо
учитывать сопротивление точечным
нагрузкам . Когда речь идет о легком
прогулочном катере или быстроходном
гоночном судне , можно и переступить
границу безопасности , при условии что
конструктор , строитель и будущий
экипаж в курсе этих слабых мест . Для
всех прочих лодок днищевой ламинат
должен выдерживать следующий тест .
И если он его не выдерживает , толщину
оболочки следует увеличить .
Изготовьте образец с характеристиками
ламината днища . Возьмите обычный
плотницкий молоток с загнутым концом
весом 600-700 г включая вес рукоятки и
длиной 300-330 мм . Человек средней
комплекции (66-82 кг) должен с силой
многократно наносить удары
закругленной стороной молотка по
наружной стороне панели , при этом
не должно быть проникновения внутрь ,
разрушения материала заполнителя или
расслоения . Поверхностные повреждения/вмятины
и разрушение наружных слоев
стеклопластика считаются нормой и
допускаются. Затем острым концом
молотка ("лапой") наносится удар
средней силы по незатронутому
предыдущим тестом участку. "Лапа"
не должна проникнуть внутрь
заполнителя более чем на 1.6 мм . Вокруг
места удара не должно возникнуть
расслоения с заполнителем . Внутренняя
оболочка и заполнитель под местом
прокола не должны пострадать . Ламинаты
для рабочих лодок и серьезных круизных
судов не должны допускать
проникновения в заполнитель вообще.
Примечание . У малых судов с
характеристикой Sn=1 и менее (упрощенно
- длиной менее восьми
метров - С.Б.) толщина наружной
оболочки сэндвича обычно составляет 2.5
мм или менее . При много меньшей толщине
оболочка не сможет пройти такой тест -
мы находимся у предела возможностей
сэндвича . В данной ситуации вам
необходимо будет самим принять решение
в зависимости от типа лодки и режима ее
эксплуатации - либо малая прочность
наружной оболочки не сильно повлияет
на безопасность , либо вам придется все
же пойти на утяжеление и удорожание ,
увеличив толщину наружного пластика на
днище .
|